Also see Dip Spin Specifications
The perfect corrosion protection solution for every kind of application.
Dip-spin offers NON-CHROME micro layer corrosion protection.
Custom Engineered Corrosion Protection
SWD will work with you and your customer to develop a tailor-made corrosion protection system for every kind of application.
Over the past few years a large number of parts have migrated from traditional electroplated finishes to Dip Spin applied engineered finishes. There are multiple reasons for this change. Whether it is corrosion protection, elimination of hydrogen embrittlement, consistent torque tension values, meeting current and future environmental regulations or other alternative finish costs, these multilayer zinc-flake coating systems are engineered to meet your requirements. Each system can be custom developed to perform exactly as needed depending on the application.
With ever greater vehicle lifespan, the corrosion protection provided on various parts needs to exceed that time frame. The Dip Spin coatings applied at SWD are at a minimum tripling the corrosion protection that would have been seen with conventional zinc electroplating. In many cases we can provide corrosion protection that will exceed 1000 hours of salt spray testing.
Whether a system is specified by the OEM or custom developed to meet your needs, SWD will work with your team to provide you the highest quality to achieve a perfect corrosion protection for your range of applications.
Elimination of Hydrogen Embrittlement
Unlike zinc electroplated parts, there is no chance for hydrogen embrittlement in parts that utilize the engineered coatings applied by SWD Inc. This is increasingly important on high strength parts such as 9.8 or parts above a Rockwell C 38. When a part is zinc electroplated, atomic hydrogen is generated on the surface of the part when it is immersed in the electrolyte solution. The hydrogen diffuses into the substrate and some remains on the surface, which may cause hydrogen-induced stress corrosion. The electroplated surface forms a barrier that locks hydrogen into the part and may not allow it to escape, thus the hydrogen is forced into voids in the part which can lead to dramatic failures. Due to the nature of zinc-flake coatings, no hydrogen is introduced from the coating or the application process.
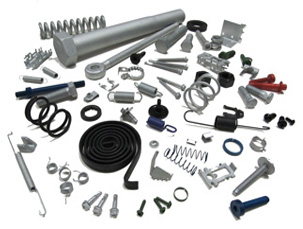
The zinc-rich coating systems used at SWD Inc. is Chromium free as well as RoHS and ELV compliant. SWD is ISO 14001 certified and is committed to continuous environmental stewardship. SWD Inc. is a charter member of the USEPA National Environmental Achievement Track, and was the only metal finishing company in the United States to be awarded a Gold level in the Strategic Goals Program.
Doerken Coating Systems
DELTA-PROTEKT® KL 100 & KL 105
DELTA®-TONE 9000 (basecoats)
DELTA-PROTEKT® KL 100 is a largely inorganic coating which forms a micro layer basecoat filled with zinc and aluminum lamella. It represents the next generation to the proven DELTA®-TONE 9000 zinc-flake coating. With a coating thickness reduced to 8µm, DELTA-PROTEKT® KL 100 achieves corrosion resistance times in excess of 600 hours.
DELTA-PROTEKT® VH 300 series (topcoats)
DELTA-PROTEKT® VH 300 is an inorganic secondary sealant which contains silicate and can be diluted with water. With a coating of only 1 to 3 µm, this product delays the effect of atmospheric substances such as moisture or oxygen and resists attack from various chemicals.
DELTA®-SEAL
DELTA®-SEAL is a highly cross-linked organic micro-layer, which makes the system highly resistant to chemical attack and is suitable for flexible work pieces. It can e used both as a sealant on an inorganic basecoat and a coating by itself on a surface after suitable pre-treatment. DELTA®-SEAL is particularly suitable for re-usable bolted joints. In addition, you can choose from a wide range of colors.
Magni 554
Developed with the OEM in mind
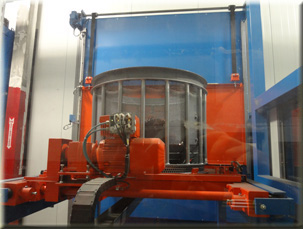
MAGNI 565
Magni 565 is a chrome-free duplex coating that combines an inorganic zinc-rich basecoat with an aluminum-rich organic topcoat. Formulated as a two-coat system and resistant to automotive fuels and fluids, Magni 565 is the preferred fastener coating of leading global automotive manufacturers. It provides superior corrosion protection and cost-effectiveness and is typically applied to externally threaded fasteners, stampings and other hardware.
Applied via dip-spin or spray application methods
Alleviates hydrogen embrittlement concerns
Excellent bimetallic corrosion resistance
Paintable
RoHS, WEEE and ELV compliant
MAGNI 501
Magni 501 is a globally available chrome-free, inorganic zinc-rich corrosion protection coating engineered for use on fasteners and other metal components. An ideal replacement coating for zinc plating and trivalent passivation, Magni 501 is applied as a thin, paintable coat that provides exceptional corrosion protection in a single layer. The result is superior performance compared to conventional zinc plating.
Alleviates hydrogen embrittlement concerns
Applied via dip-spin with tilt and tumble to minimize recess fill
Excellent protection against aluminum
Consistent torque-tension relationship
Resistant to automotive fuels and fluids
RoHS, WEEE, ELV and REACH compliant